Continuous production of biopolymers
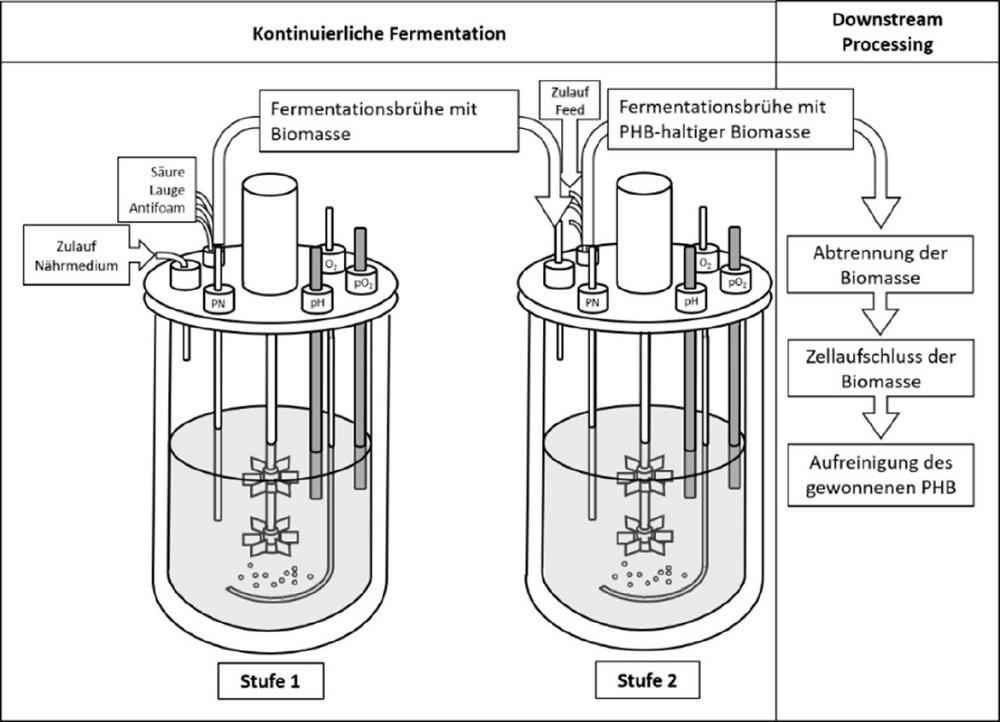
Breaking News:
Samstag, Feb. 22, 2025
Bio-based and biodegradable thermoplastics are becoming increasingly important in the wake of the growing importance of sustainable management. However, the production processes are not yet at the same level of efficiency as traditional polymers. The difficulty usually lies in extracting the polymer from the remaining so-called fermentation broth.
In the recently completed ModiBioPol research project, the SKZ Plastics Center in Würzburg and the research group led by Prof. Stute from the Chair of Bioprocess Engineering at Nuremberg Institute of Technology have pooled their resources and achieved notable successes in terms of more efficient PHB production processes.
The biopolymer polyhydroxybutyrate (PHB) is currently produced using the so-called fed-batch process, which is a discontinuous process. The challenge for the scientists at the two institutes was to make this process possible in a continuous process and at the same time achieve a uniform chain length of the polymers.
To this end, a continuous production process was developed that optimizes the fermentation conditions and influences the polymer structure by controlling the residence time and the synthesis parameters in the reactor. In addition, suitable preparation and extraction methods are being researched in order to reduce undesirable degradation of the polymer chains.
The biopolymers produced were intensively tested in the course of the project, the process was evaluated techno-economically at the SKZ and even the complete life cycle of the polymers was considered and compared with conventional polypropylene in terms of the ecological footprint.
“We are very satisfied with the results of ModiBiopol. We have succeeded in enabling the continuous biosynthesis of PHB for more than 1,000 hours. At the same time, we are also so satisfied with the technical/economic and ecological findings that we are aiming for follow-up projects in the near future,” explains Dr. Oliver Tröppner, Group Leader Materials Development at SKZ.
The core of the successful efficiency improvement was the optimization of the process steps in the so-called purification (downstream processing) of the synthesized polymers. The illustration shows the schematic sequence of the optimized manufacturing process.
The SKZ is climate protection company and a member of the Zuse Association. This is an association of independent, industry-related research institutions that pursue the goal of improving the performance and competitiveness of industry, especially SMEs, through innovation and networking.
FSKZ e. V.
Friedrich-Bergius-Ring 22
97076 Würzburg
Telefon: +49 931 4104-0
https://www.skz.de