Effiziente Zellproduktion: Forschungsteam skaliert nachhaltige Direktbeschichtung von LFP-Elektroden
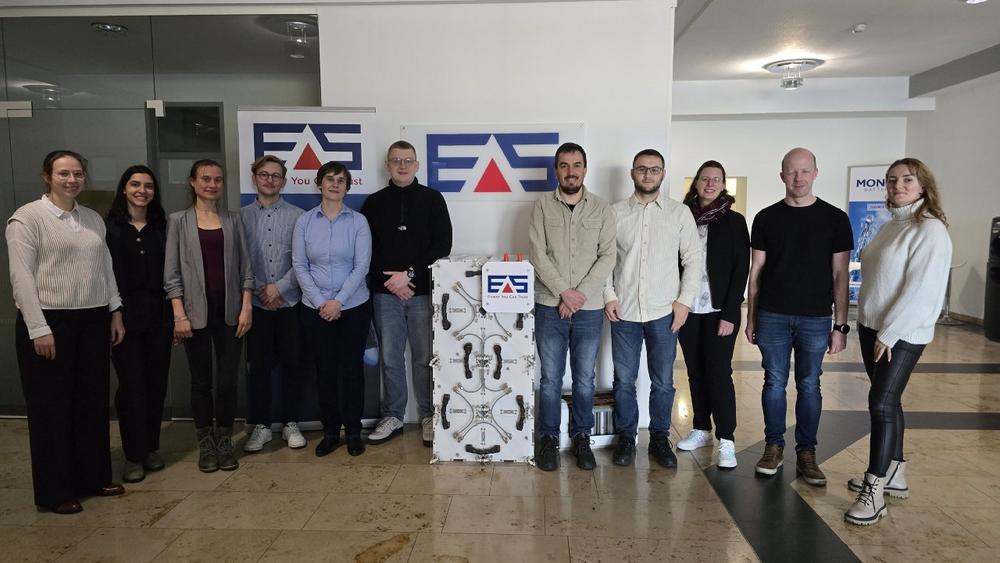
Breaking News:
Logistische Prozesse passgenau digitalisieren, sinnvoll vernetzen und dynamisch weiterentwickeln
Kurios & komplex: FRC widmet dem Schnabeltier eine australische Sonderedition
Effiziente Zellproduktion: Forschungsteam skaliert nachhaltige Direktbeschichtung von LFP-Elektroden
Fasnetsumzüge in St. Georgen und Gundelfingen: Streckenänderungen
Dienstag, Feb. 11, 2025
Manugy, Matthews International, das Fraunhofer-Institut für Keramische Technologien und Systeme IKTS, die Fraunhofer-Einrichtung Forschungsfertigung Batteriezelle FFB und EAS Batteries optimieren und ein Direktextrusionsverfahren sowie das dazugehörige Anlagenkonzept vom Pilot- auf den industriellen Maßstab und ergänzen es mit effizienzsteigernden Innovationen – bis hin zu einer Technologie für die simultan beidseitige Direktbeschichtung der Elektroden.
Das Forschungsprojekt „SkaleD – Skalierung der extrusionsbasierten Direktbeschichtung“ wird mit rund 2,1 Millionen Euro aus den Mitteln des „Sondervermögen Klima- und Transformationsfonds“ des Bundesministeriums für Bildung und Forschung (BMBF) unterstützt (Förderkennzeichen 03XP0631A-D). Das Gesamtvolumen beträgt 2,8 Millionen Euro. EAS Batteries koordiniert das Forschungsprojekt.
Skalierte Technologie – umweltverträglich, optimiert und inlinefähig
Neuartige lösungsmittelreduzierte Beschichtungsverfahren sind der Schlüssel, um die Produktion von Elektroden nachhaltig, effizient und gesundheitsverträglich zu gestalten. Das Forschungsprojekt „SkaleD“ setzt auf das im Vorläufer-Projekt „OptiEx“ entwickelte Verfahren der Direktextrusion auf, um die innovative Technologie massenfertigungstauglich zu gestalten. Das Verfahren stellt eine ressourcenschonende Alternative zum bisher etablierten Prozess dar und überwindet den technologischen Engpass dieses entscheidenden Fertigungsschritts in der Produktion von Batterien. Der Forschungsverbund wird die gesamte Prozesskette anpassen und verbessern. Dies gilt insbesondere für die Beschichtungsbreite und Prozessgeschwindigkeit sowie für damit einhergehende Optimierungen der Anlagentechnik und Rezepturen. Ebenso steht die Inlinefähigkeit im Fokus, sodass Anlagentechnik und Verfahren an vor- und nachgelagerte Prozesse gekoppelt werden können. Zudem soll in diesem Projekt erstmals – zunächst in Form einer Machbarkeitsstudie – eine simultane doppelseitige Beschichtung realisiert werden, welche die Prozessgeschwindigkeit signifikant erhöhen kann.
Geförderte Batterieforschung – wettbewerbsfähig und zukunftsweisend
Um in Deutschland und Europa insbesondere gegenüber asiatischen Märkten wettbewerbsfähig zu bleiben, muss der Preis pro Kilowattstunde in Europa produzierter Zellen sinken. Dies gelingt durch die Etablierung innovativer Fertigungsverfahren. „Wir freuen uns, dass die Bedeutung einer effizienten Massenproduktion von Batteriezellen von Seiten des Bundes erkannt und unser Forschungsbeitrag gefördert wird“, sagt EAS-Geschäftsführer Michael Deutmeyer. „Das ist in Zeiten der Budgetkürzungen nicht selbstverständlich und hebt die Relevanz unserer Entwicklungstätigkeit noch einmal hervor. Zugleich ist dies ein dringender Appell, den gesamten Standort Deutschland in der Umsetzung der Energiewende mit einem neuen, deutlich höheren Etat für die Zell- und Batterieforschung zukunftsweisend zu unterstützen und den jetzt eingeschlagenen Weg der Überbrückungsfinanzierung konsequent in diese Richtung fortzuführen.“
Industriestandort Deutschland – nachhaltig, innovativ und kosteneffizient
Das Bewusstsein für Nachhaltigkeit und die Anforderungen an kosteneffiziente Batteriesysteme wachsen weltweit kontinuierlich. Die angestrebten Erkenntnisse im Forschungsprojekt „Skale D“ entsprechen diesem Bedarf und sichern die langfristige Weiterentwicklung der Batteriezellproduktion. Damit stärken die neuen Kompetenzen den Industriestandort Deutschland sowie den europäischen Wirtschaftsraum. Die entwickelten Anlagen und Prozesse eröffnen neue Absatzmärkte – bis hin zur Skalierung des Konzepts von der industrieähnlichen Umgebung auf einen Gigafactory-Maßstab. Damit schaffen die Projektergebnisse vielseitige Verwertungsmöglichkeiten und internationale Wettbewerbsfähigkeit. Das Forschungsprojekt hat eine Laufzeit von drei Jahren und endet am 31. Dezember 2027.
Über EAS Batteries
Großformatige Wickelzellen, LFP als sichere Zellchemie, energiesparsame Extrusion und eine effiziente Kontaktierungsmethode gehören zu den zugkräftigen Ideen eines Vierteljahrhunderts EAS-Geschichte. Als hochspezialisierter Nischenanbieter entwickelt EAS seit 25 Jahren innova-tive Zell- und Batterielösungen am Produktionsstandort Nordhausen – darunter extrem robuste und leistungsfähige Zellen für Anwendungen in den Bereichen Maritime Industrie, Raumfahrt, Luftfahrt, NRMM (Non-Road Mobile Machinery) und in der Automobilindustrie. Die Marke EAS ist aus der GAIA Akkumulatorenwerke GmbH hervorgegangen, gegründet 1996 in Nordhausen. Seit Juni 2017 ist die EAS Batteries GmbH Teil der Monbat Gruppe.
Über Manugy
MANUGY ist ein Maschinen- und Anlagenhersteller für modulare, klein- bis mittelskalige, hoch-automatisierte Produktionslinien von Energiespeichersystemen mit besonderem Fokus auf die Batterietechnik. Die MANUGY vereint Produkt-, Prozess- sowie Maschinen- und Anlagenwissen, um Kunden zur Fertigung hochwertiger Next-Gen-Batteriezellen zu befähigen. Als Ausgrün-dung des Fraunhofer IPT knüpft es an Entwicklungen einer flexiblen, modularen und anpassba-ren Maschinenarchitektur an. In den vergangenen Jahren wurde diese Maschinenarchitektur insbesondere für kontinuierliche Rolle-zu-Rolle (R2R) und diskrete Assemblier-Anlagen opti-miert.
Über Matthews International
SAUERESSIG als Teil der Matthews International GmbH ist ein führender und innovativer Kom-plettanbieter von Kalander-, Präge-, und Rotationsverarbeitungssystemen in Standard- und Sonderausführungen. Das Produktportfolio umfasst sowohl komplette Fertigungslinien als auch Einzelanlagen zum Prägen, Veredeln, Glätten, Perforieren und Kalibrieren bahnförmiger Materia-lien. Neben individuellen Lösungen für die Converting-Industrie entwickelt und fertigt Matthews Engineering zukunftsweisende Anlagen für die Herstellung von Batteriekomponenten, und bil-det dabei die komplette Prozesskette von der Entwicklung über die Fertigung bis zur Installati-on und Inbetriebnahme der Produktionslinien ab. Umfassende Testmöglichkeiten und vielseiti-ges Laborequipment bilden die Schnittstelle zwischen Labor und Großserienfertigung.
Über Fraunhofer-Institut für Keramische Technologien und Systeme IKTS
Das Fraunhofer IKTS entwickelt keramische Hochleistungswerkstoffe, industrierelevante Her-stellungsverfahren sowie prototypische Bauteile und Systeme in vollständigen Fertigungslinien bis in den Pilotmaßstab. Ein breites Spektrum an Technologien der Werkstoffdiagnose und -prüfung trägt maßgeblich zur Qualitätssicherung von Produkten und Anlagen unserer Kunden bei. Im Fokus stehen nachhaltige und wirtschaftliche Lösungen für Ressourcenschonung, Ener-giewende und Digitalisierung.
Über Fraunhofer-Einrichtung Forschungsfertigung Batteriezelle FFB
Die Fraunhofer-Einrichtung Forschungsfertigung Batteriezelle FFB ist eine Einrichtung der Fraunhofer-Gesellschaft am Standort Münster. Ihr Konzept sieht eine Kombination aus Labor- und Produktionsforschung für unterschiedliche Batteriezellformate – Rundzelle, prismatische Zelle und Pouchzelle – vor. Die Mitarbeitenden der Fraunhofer FFB erforschen je nach Bedarf einzelne Prozessschritte oder die gesamte Produktionskette. Am Standort Münster wird eine Infrastruktur geschaffen, mit der kleine, mittlere und Großunternehmen, aber auch Forschungs-einrichtungen, die seriennahe Produktion neuer Batterien erproben, umsetzen und optimieren können. Im Rahmen des Projektes »FoFeBat« fördern das Bundesministerium für Bildung und Forschung und das Land Nordrhein-Westfalen den Aufbau der Fraunhofer FFB mit insgesamt rund 820 Millionen Euro. Dabei fördert der Bund die Fraunhofer FFB mit bis zu 500 Millionen Euro für Forschungsanlagen und -projekte, das Land Nordrhein-Westfalen investiert rund 320 Millionen Euro für Grundstücke und Neubauten.
EAS Batteries GmbH
Lokomotivenstraße 21
99734 Nordhausen
Telefon: +49 (3631) 46703-0
Telefax: +49 (3631) 46703-228
http://www.eas-batteries.com