Common Pitfalls: Avoiding Steelmaking Defects
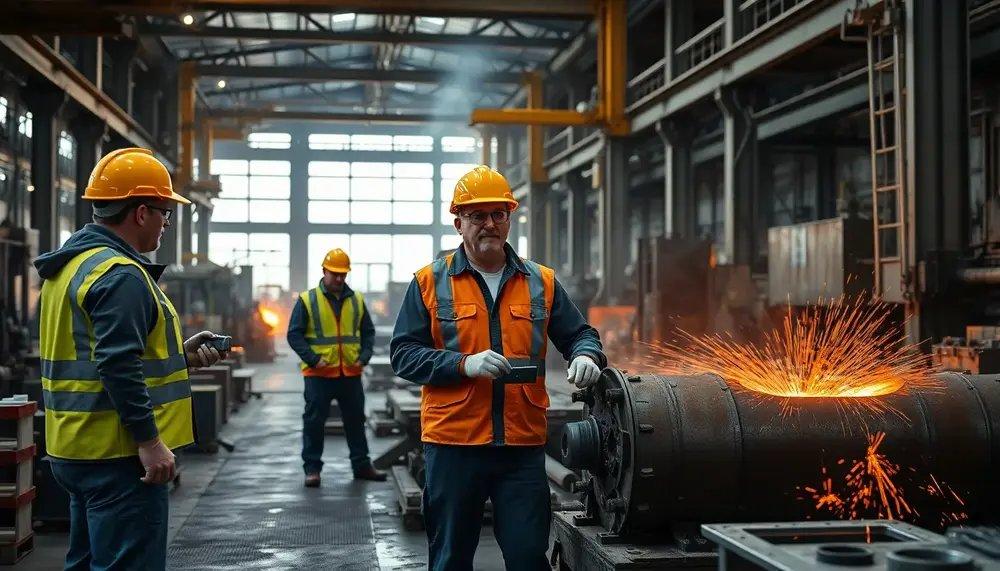
Breaking News:
Montag, Jan. 20, 2025
Steelmaking is a fascinating yet complex process, and like any intricate art, it comes with its own set of challenges. Among these, defects are the sneaky culprits that can mar the beauty and integrity of the final product. But what exactly are these defects, and why do they matter so much?
Imagine crafting a masterpiece, only to find it tarnished by unexpected flaws. That’s the reality for steelmakers when defects creep in. These imperfections can pop up at any stage, from casting to rolling, and each has its own unique signature. They might be as subtle as a whisper or as glaring as a shout, but either way, they can’t be ignored.
In the world of steel, defects aren’t just a cosmetic issue. They can affect the strength, durability, and even the safety of the steel. So, understanding these pitfalls isn’t just about quality control; it’s about ensuring that the steel we rely on every day is up to the task.
In this guide, we’ll dive into the nitty-gritty of steelmaking defects, exploring their origins, impacts, and most importantly, how to steer clear of them. Whether you’re a seasoned pro or a curious newcomer, there’s always something new to learn in the quest for flawless steel.
Common Types of Surface Defects in Steel
Steel, despite its robust nature, can sometimes show signs of wear and tear even before it leaves the factory. These are known as surface defects, and they can be quite the nuisance. Let’s take a closer look at some of the usual suspects that tend to pop up during steel production.
Each of these defects has its own tale to tell, often hinting at what went awry during production. By identifying these common issues, steelmakers can better pinpoint where things might have gone off track and take steps to correct them. After all, a stitch in time saves nine, right?
Understanding the Causes of Steel Defects
Understanding why steel defects occur is like being a detective on a mission. Each defect has its own backstory, and uncovering these tales can help prevent future mishaps. So, what are the usual culprits behind these steelmaking woes?
Each of these causes tells a story of what might have gone wrong during the steelmaking process. By piecing together these clues, manufacturers can take proactive steps to avoid these pitfalls. After all, knowing the cause is half the battle won, isn’t it?
Impact of Defects on Steel Quality
Steel defects, though sometimes small, can have a mighty impact on the quality of the final product. Imagine building a house on a shaky foundation; that’s what defects can do to steel. They compromise not just the appearance but also the performance and safety of the material.
Firstly, defects can weaken the structural integrity of steel. For instance, cracks and porosity can act like tiny fault lines, making the steel more susceptible to breaking under stress. This is particularly concerning in applications where strength is non-negotiable, like in construction or automotive industries.
Then there’s the issue of durability. Defects such as inclusions and laminations can accelerate wear and tear, reducing the lifespan of the steel. It’s like buying a new car only to find it rusting away sooner than expected.
Moreover, surface defects can lead to additional costs. They often require rework or scrapping of the affected material, which is both time-consuming and expensive. This can affect the bottom line, especially in large-scale production environments.
Finally, let’s not forget the aesthetic aspect. Surface defects like black marks or bare spots can make the steel look unappealing, which is a big no-no for products where appearance matters, such as consumer goods or architectural elements.
In essence, defects are like the hidden gremlins of steel production, lurking beneath the surface, ready to cause trouble. Addressing them is crucial to ensuring that the steel not only meets but exceeds quality expectations. After all, nobody wants to build their dreams on shaky ground, right?
Effective Strategies to Prevent Defects
Preventing defects in steelmaking is like playing a strategic game of chess; every move counts. By implementing effective strategies, manufacturers can stay one step ahead of potential issues. Here are some key tactics to keep those pesky defects at bay:
By weaving these strategies into the fabric of the production process, manufacturers can create a robust defense against defects. It’s about being proactive rather than reactive, ensuring that the steel produced is not just good, but exceptional. After all, a stitch in time really does save nine, doesn’t it?
Case Studies: Avoidance of Steelmaking Defects in Practice
Sometimes, the best way to learn is by example. Let’s dive into a couple of real-world case studies where steel manufacturers successfully tackled defects, turning potential pitfalls into triumphs.
Case Study 1: The Buildup Battle
A leading steel plant faced recurring issues with zinc buildup, which was causing wavy surfaces and spooled edges. After a thorough investigation, they discovered that the air knife above the zinc bath was frequently clogging. The solution? They implemented a rigorous cleaning schedule and upgraded the air knife system to a more advanced model. This proactive approach led to a significant reduction in buildup, improving both the quality and appearance of their steel products.
Case Study 2: Cracking the Crack Problem
Another steel manufacturer was struggling with cracks forming during the heat treatment process. These defects were compromising the strength of their steel, leading to costly reworks. By revisiting their heat treatment protocols and investing in state-of-the-art temperature control systems, they managed to eliminate the cracks. This not only enhanced the durability of their steel but also boosted their production efficiency.
Case Study 3: Inclusion Intrigue
A company producing high-grade steel for the automotive industry found that inclusions were affecting the finish of their products. They decided to overhaul their raw material sourcing, opting for higher purity inputs. Additionally, they introduced a more stringent inspection process using advanced scanning technology. The result? A dramatic decrease in inclusions and a smoother, more consistent product finish.
These case studies highlight the importance of identifying the root causes of defects and taking decisive action. By learning from these examples, other manufacturers can adopt similar strategies to enhance their own production processes. It’s all about turning challenges into opportunities for improvement.
Conclusion: Ensuring Quality in Steel Production
In the grand tapestry of steel production, ensuring quality is the golden thread that holds everything together. It’s not just about creating a product; it’s about crafting something that stands the test of time, both in function and form. Defects, while pesky, are not insurmountable obstacles. Rather, they are opportunities for learning and improvement.
By understanding the common types of defects and their causes, manufacturers can take a proactive stance. It’s about implementing effective strategies, from regular maintenance to advanced training, and learning from real-world examples. Each step taken towards defect prevention is a step towards excellence.
Ultimately, the goal is to produce steel that is not only strong and durable but also aesthetically pleasing. This requires a commitment to quality at every stage of the production process. With the right approach, manufacturers can ensure that their steel products meet the highest standards, ready to build the future.
So, as we wrap up this exploration of steelmaking defects, remember: quality isn’t just a box to tick; it’s a promise to deliver the best. And in the world of steel, that’s a promise worth keeping.
Die Provimedia GmbH ist ein Online-Verlag mit Sitz in der Region Stuttgart. Wir schaffen wertvolle Informationen in unterschiedlichen Branchen um Wissen schnell und einfach zugänglich zu machen. Wir haben uns auf übersichtliche Webseiten und Auffindbarkeit von Informationen spezialisiert.
Provimedia GmbH
Weidenweg 12
74321 Bietigheim-Bissingen
Telefon: +49 (7142) 3442727
Telefax: +49 (7142) 2279985
http://provimedia.de