Capturing hidden air leaks in time prevents serious incidents and saves costs at a pharmaceutical plant
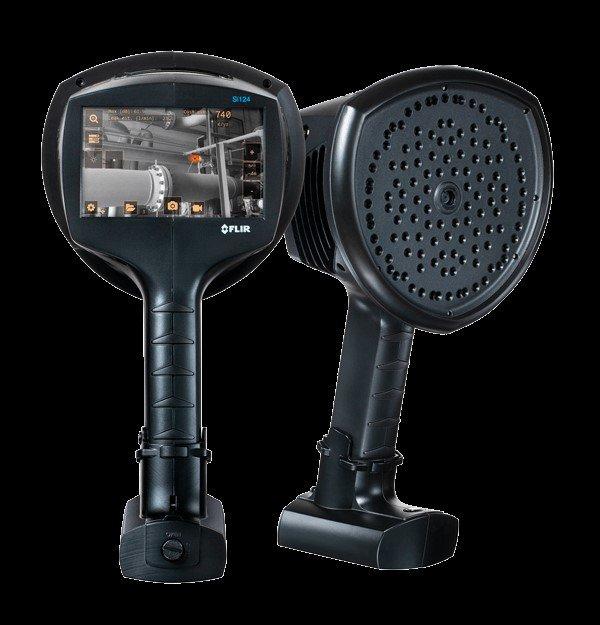
Breaking News:
Freitag, Nov 1, 2024
ENSURING OPERATIONAL CONTINUITY AND PREVENTING ACCIDENTS
An international pharmaceutical company discovered that an acoustic camera is a reliable, fast, and easy-to-use predictive maintenance method for detecting hidden air leaks in the plant area.
Air leaks are a common problem in industrial environments. According to studies on compressed air system leaks, the average leakage rate is around 25%, but some facilities are losing up to 80% of their compressed air through leaks. If not detected and addressed on time, these leaks may end up causing additional costs, unplanned stoppages, and even potential safety hazards. Locations especially prone to air leaks in plants and manufacturing facilities include equipment pipelines, pipes, valves, and equipment gaps, where they are generally invisible to the naked eye and only traceable with specialized condition monitoring equipment.
ENSURING OPERATIONAL CONTINUITY AND PREVENTING ACCIDENTS
An international pharmaceutical and biotechnology company was concerned with compressed air leaks and had been looking for an effective, yet easy-to-use solution for their timely detection. As speed, accuracy, and reliability were high on the company’s list of requirements for leak detection, they decided to try an acoustic camera to perform valve inspections and leak detections to locate compressed air, steam, gas, and vacuum leaks within its facilities. The company was quickly impressed by how effectively the device was able to capture hidden leaks, scanning large areas at a time. The device was not only able to pinpoint the exact location of the leak, but also provided leak size and cost calculations which enabled the company to make data-based plans for the maintenance and repairs of their equipment.
THE PERFECT SOLUTION FOR FAST AND RELIABLE AIR LEAK INSPECTIONS
By using an acoustic camera for their regular predictive maintenance regime, the pharmaceutical company has been able to prevent potential safety issues and ensure the continuity of their operations by detecting air and gas leaks in the plant area. In addition to the obvious benefits of time, cost and energy savings, the company has been pleasantly surprised at how easy the device has been to incorporate into the maintenance cycle with minimal training.
BENEFITS OF AN ACOUSTIC CAMERA FOR AIR LEAK DETECTION
• Saves time, energy and costs by locating hidden compressed air leaks in time.
• Ensures operational continuity through early detection of air and gas leaks.
• Scans large areas quickly and pinpoints critical problems accurately.
• Requires minimal training and is easy to incorporate into the maintenance cycle.
• Provides real-time results and actionable data for maintenance and repair plans through machine-learningdriven analytics.
For more information about thermal imaging cameras or about this application please visit: www.FLIR.com/si124
Teledyne FLIR, a Teledyne Technologies company, is a world leader in intelligent sensing solutions for defense and industrial applications with approximately 4,000 employees worldwide. Founded in 1978, the company creates advanced technologies to help professionals make better, faster decisions that save lives and livelihoods. For more information, please visit www.teledyneflir.com or follow @flir.
Teledyne FLIR
Schwieberdinger Straße 60
71636 Ludwigsburg
Telefon: +49 (7141) 488817-0
Telefax: +49 (7141) 488817-99
http://www.flir.de/MV