The Path to Automation
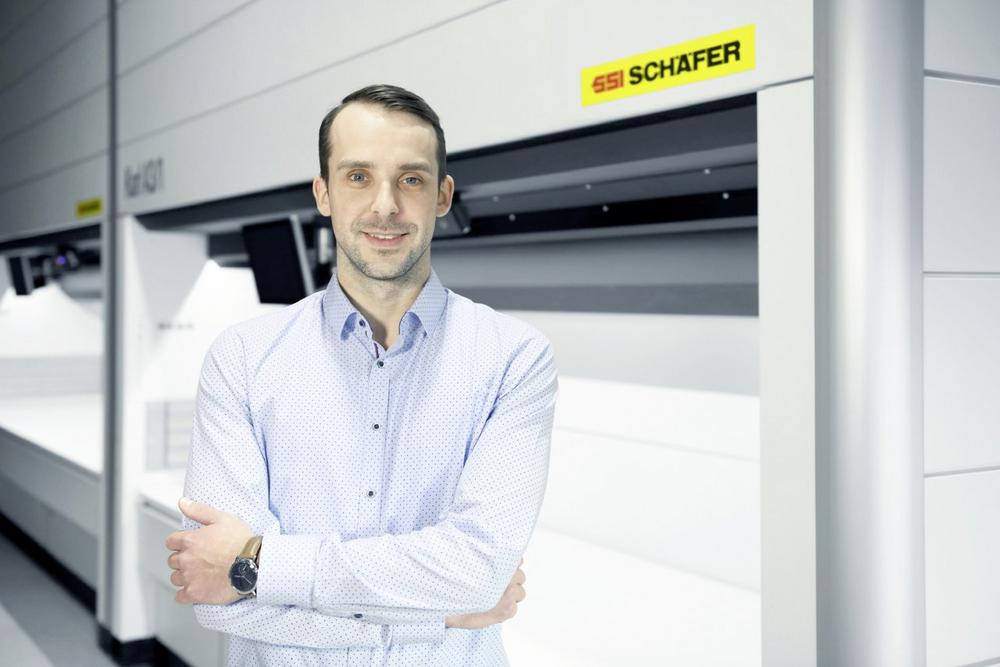
When C+C Krug contacted SSI Schaefer, the new warehouse was under construction. For this reason, it was high time to plan the storage equipment for the new warehouse. The medium-sized company C+C Krug GmbH headquartered in Ottendorf-Okrilla, Saxony, Germany, was founded in 1991 and specializes in plastic electroplating. Sophisticated coating systems are realized from parts construction to sample processing to serial production. C+C Krug produces coating systems for automobile interior and exterior in high gloss as well as customized in matt tones.
Due to a positive sales development, the production volume of C+C Krug considerably increased in the past year. The number of projects rose and therefore stock also increased because more raw materials had to be available. The existing warehouse could no longer accommodate the necessary stock. Along with the new building, warehousing was also intended to change in order to minimize searching and picking times. The existing warehousing system caused long searching times and sometimes even affected the production times. The construction of the new building had several objectives. Gaining more space for raw material, finding suitable, modern warehouse equipment for the large number of items and making processes in warehouse and production more efficient – ideally using semi-automation. These were the requirements that C+C Krug communicated to SSI Schaefer using the contact form on the website. “The fast response time of SSI Schaefer was unique,” says Christian Krause, Head of Logistics at C+C Krug GmbH. “Only one or two days after my inquiry, I got a call from the responsible sales representative and a week later we scheduled an on-site visit.”
Shortly afterwards, the companies were in the projecting phase. For this purpose, the SSI Schaefer experts first gained an overview of the number of items and the dimensions of the components, and so determined the overall volume. Among the components on stock at C+C Krug are accent moldings, outer moldings and other design elements to be applied on the inside or outside of cars. Some of the components are bulk goods of approx. 1,000 to 2,000 parts per small load carrier). Furthermore, the entire processes were monitored and analyzed. Based on time studies, intralogistics emerged as the medium for process optimization. If the raw material did not arrive at the production work station in time, idle times occurred. SSI Schaefer presented the customer three different logistics concepts, based on a manual, semi-automated or automated solution. C+C Krug opted for a solution consisting of three SSI LOGIMAT storage lifts, a bin and carton conveying system, two automated guided vehicles (AGV) type WEASEL and two transfer locations. The warehouse concept has been designed for expansion to be carried out over various construction stages.
The three SSI LOGIMAT Vertical Lift Modules (VLM) are located at the face side of the approx. 620 m² hall and ensure efficient, reliable processes – there is also enough room for nine to ten further small parts lifts that will follow. Modernization in stages is important for C+C Klug. “We want to keep the investment for each expansion stage manageable and learn how to handle modern systems so that we can plan further steps according to requirements,” explains Mr. Krause. Opting for the LOGIMAT storage lift, C+C Krug receives a combined warehousing and picking solution. The storage tower resembles an oversized drawer cabinet with two rows of trays – one in the front and one in the rear row. Picking is done according to the goods-to-person principle. Between the two rows is a lift, which pulls out the individual trays and moves them to the respective position of the opening. What makes the tray system particularly interesting is the optimum use of the hall height:
There is only little room left between storage lift and ceiling. The machine height is customizable, so LOGIMAT fits perfectly in the hall in Ottendorf-Okrilla which is 8 m high. The machines are each equipped
with 39 trays sized 3,625 mm x 815 mm. “Furthermore, the tray lift scores with its compact design and condensed storage on smallest footprint,” says Rico Bär, SSI Schaefer sales representative. “This reduces the walking distances for the employees considerably.” The C+C Krug product range includes about 200 items; the number is constantly growing. About 50% of these items can be accommodated in the storage lifts. The next expansion stage will cover storage of the remaining items.
As an additional option for the small parts lift, C+C Krug chose a locking mechanism of the retrieval opening to protect the goods against dust and soiling, and additional illumination of shaft and control cabinet. Furthermore, the option LOGIBAR offers a confirmation light barrier under the operator opening. This function serves to acknowledge the picking order/tray change directly under the access opening in the lift system. This leads to an increased picking speed and less walking times. The software solution WAMAS® LOGIMAT oversees the item management for the three storage lifts. The option WAMAS LOGIMAT Orderhandling connects them flexibly to the superordinate customer ERP system. The advantage is that stock and orders are automatically synchronized in ERP and WAMAS LOGIMAT. For employees, it means paperless working and no more manual booking. Additionally, it is easy to form dynamic picking areas. “It was relatively easy to group components according to colors, customers and form areas using the WAMAS LOGIMAT software,” states Mr. Krause. “Forming areas facilitates achieving a higher picking performance.” Depending on work load, one, two or three employees can pick in parallel at the tray lifts.
The WEASEL as AGVs connect the storage and the production area barrier-free and safe for persons. The use of surfaces and space remains flexible. The ERP system sends orders to the VLM. WAMAS LOGIMAT compiles the corresponding items for picking according to the FIFO principle. A warehouse operator takes the carton or container off the supplied tray and places it onto the conveying section at the long side of the hall. The first meters of the conveying system have been designed as inclined conveyor followed by a driven conveying system. At the end of the section is the automatic transfer conveyor for the AGVs. The transfer conveyor can accommodate and buffer a variety of bins to distribute them in a dynamic process among the available vehicles. For this purpose, the WEASEL goes under the transfer conveyor to catch the transport unit.
The WEASEL is the perfect solution for transporting containers and cartons weighing up to 35 kg. The AGVs navigate along a visual driving track. The WEASEL can achieve a speed of up to 1 meter per second. The fleet controller or manager handles the control and optimization of all transport orders. “Our AGVs can be flexibly adapted to changed market conditions,” explains Thomas Lamprecht, SSI Schaefer project manager. “For instance, the number of vehicles can be increased according to performance requirements.”
If production planning requires a component series, the production employee requests a WEASEL by pushing a button. The WEASEL takes the small load carrier from the transfer conveyor and transports it to the manual transfer location in production. There, an employee collects the bin or carton and takes it to the corresponding work station. In production planning, the components are put on product carriers for coating.
Thanks to the new, semi-automated solution, which was accepted in September 2019, C+C Krug achieved considerable time savings in the provision of components. “We could increase the availability speed by 90%, while picking times were reduced by 50%,” resumes Mr. Krause. “In total, we look back at great cooperation with SSI Schaefer, communication went extremely well in this cooperation. We plan the next expansion for the near future.
The SSI Schaefer Group is the world’s leading provider of modular warehousing and logistics solutions. It employs approximately 10,500 people at its group headquarters in Neunkirchen (Germany), at eight domestic and international production sites, and at approximately 70 worldwide operative subsidiaries. Across six continents, SSI Schaefer develops and implements innovative industry-specific answers to its customers‘ unique challenges. As a result, it plays a key role in shaping the future of intralogistics.
SSI Schaefer designs, develops and manufactures systems for warehouses, industrial plants, workshops and offices. Its portfolio includes manual and automated solutions for warehousing, conveying, picking and sorting, plus technologies for waste management and recycling. In addition, SSI Schaefer is now a leading provider of modular, regularly updated software for in-house material flows. Its IT team, with a headcount in excess of 1,100, develops high-performance applications, and provides customers with in-depth advice on the intelligent combination of software with intralogistics equipment. SSI Schaefer’s broad IT offering, including its own WAMAS® and SAP products, delivers seamless support for all warehouse and material flow management processes. Solutions from SSI Schaefer improve the productivity and efficiency of customer organizations – not least through the highly precise monitoring, visualization and analysis of operational metrics for proactive intralogistics management.
SSI Schaefer offers highly sophisticated, turnkey systems. As an international player, it can deliver one-stop solutions to all four corners of the earth. Its comprehensive portfolio encompasses design, planning, consulting, and customer-specific aftersales services and maintenance.
SSI SCHÄFER
Fritz-Schäfer-Strasse 20
57290 Neunkirchen / Siegerland
Telefon: +49 (2735) 70-1
Telefax: +49 (2735) 70-396
http://www.ssi-schaefer.de